As an Amazon Associate, this site earns commissions from qualifying purchases. For more details, click here.
An air compressor is a versatile device that can be used to inflate tires and supply air pressure for various building projects and tools in workshops and garages. Usually they run on electricity or gas, but what inverter size would you need to run an air compressor?
A 500 watt inverter can run a basic 12V 15 amp air compressor. A 1 HP 120V air compressor however, will require a 3000 watt inverter.
Calculate Air Compressor Inverter Power Requirements
There are several types of air compressors, ranging from portable units for home use and large, stationary systems installed in factories. We are going to focus on the devices used at home and workshops.
To calculate the inverter size for your air compressor:
Total watts per hour + 25% = inverter size
If your air compressor uses 350 watts;
350 + 25% = 437
Round that off to 500 watts for your inverter. We suggest a pure sine wave system like the ALLWEI 500W Inverter for the best results. Once plugged in your compressor will start running.
Because compressors have varied uses, their capacity and specs have a broad range. On the one hand you have the basic 12V air compressor used to inflate tires and small tools. These usually draw 15 to 30 amps or about 180 to 360 watts.
At the high end are air compressors designed for heavy duty use in workshops. These devices usually run on 120V, drawing 15 amps or 1500 watts. This is different from the 15 amps drawn by small compressors as those run on 12V, not 120V.
So the first thing you need to do is check the compressor voltage requirement. Portable air compressors can run on 12V and are suitable for inflating bike and vehicle tires. The larger ones run on 120V and require much more power.
Air Compressor Inverter Size Guide
Here is a chart showing the most common air compressor types and inverter sizes. If you are still not sure, check the label or product manual. There will be information on the watts, amps, volts etc. Use it as a guide to determine what type of solar power system will be required, factoring in your own personal usage.
Compressor Type | Power Consumption | Recommended Inverter Size |
---|---|---|
12V Air Compressor 120 psi | 200-360W | 500W |
120V Pancake 3 Gallon 120 psi | 1200W | 2500W |
120V Hot D0g 150 psi | 1200W | 3000W |
120V Twin Stack 4 Gallon 120 psi | 1500W | 3000W |
1 / 2 HP | 1000W | 2000W |
1 HP | 1500W | 3000W |
1 1/2 HP | 2200W | 5000W |
2 HP | 2800W | 6000W |
The first thing you will notice with the chart is the wide range. The reason is the term air compressor applies to a huge selection of devices. All of them have the same basic function, but the specs differ significantly.
The most common inverter sizes are 1000, 2000, 3000, 4000 and 5000 watts. If your device needs 2500 watts, buy a 3000 watt inverter. When it comes to inverters and solar power in general, it is always better to overestimate your needs.
The 25% buffer is the minimum. Buy a larger inverter if you expect to overshoot your power usage. You will definitely need a bigger system if you are going to use the compressor with several tools.
Check the specs of each air compressor before buying. You do not want to end up with an underpowered device. But you also don’t want to buy a 2 HP system if you just need to inflate bicycle tires.
How to Calculate Air Compressor Inverter Usage
To calculate the inverter usage of an air compressor, convert the amp draw into watts and add 25%. The result is the inverter size needed to start the device. To determine the exact watts used, you have to calculate its runtime.
Like a solar powered welder, an air compressor cycles on and off. But it is easy enough to figure out how much power the device uses.
If you have a 12V 15 amp compressor, it can use up to 180 watts an hour. But only if you actually use the device for 60 minutes. But if you use the device to inflate tires, that will only take a few minutes or seconds. It will consume power yes, but not 120 watts.
It is a different story if you use the air compressor with some power tools. Let us assume you have a 12V 30 amp compressor that runs for 3 hours a day.
30 amps x 12V = 360 watts
360 watts x 3 hours = 1080 watts
So your air compressor consumes over 1000 watts in three hours. At the very least you should get a 1500 watt inverter, though we recommend 2000 watts because it is better to have extra power available.
You can use the same steps for larger devices. A 120V 15 amp air compressor consumes 1800 watts an hour.
120V x 15 amps = 1800 watts
Run the device for 2 hours and that is 3600 running watts. Its starting wattage will be double that at 7200 watts. You will need at the very least an 8000 watt inverter.
Inverters are not 100% efficient, and energy loss can be up to 15% in some cases. By opting for a larger system you can run a compressor without pushing the inverter to the limit.
All of these sounds like a lot of watts consumption and that is true. Running power tools on an inverter requires a large system including the inverter. This also means you must have a sizable battery bank to power the apparatus.
What Type of Inverter is Needed For a Compressor?
A modified sine wave inverter is fine for 12V air compressors and simple tasks. A pure sine wave inverter is recommended for heavy duty air compressors.
If you just need a tire inflator a basic pneumatic device, a modified sine wave inverter will work. Of course you should check the product manual if it requires a specific inverter type. But usually a modified sine wave is good enough.
More powerful inverters with 1 HP to 2 HP power are optimized for pure sine wave inverters. These large motors are designed to run complex tools, which require pure sine wave. If your workshop or home needs a 2 HP compressor, go with pure sine.
Pure sine wave inverters cost more than modified sine. But they are made specifically for high end motors, power tools and appliances. In short they are designed for optimum performance.
How Many Batteries Will My Inverter Need to Run a Compressor?
Most air compressors run on gas or electrical power. If you want to run them on an inverter battery, it must provide sufficient energy to keep the device running.
Since air compressor power is measured in amps it is easy to figure out how much you need. A 12V 15 amp air compressor needs a minimum 15ah battery power. For a deep cycle battery you should use a 30ah because it needs to be recharged at 50%.
If the power specs is listed in watts, divide watts by the voltage to find its amps. A 150 psi air compressor that pulls 120 watts an hour needs 12.5 amps. Round that off to the nearest available battery size, that would be 20ah.
The conversion formulas are:
Amps x volts = watts
Watts / volts = amps
The battery calculations given here pertain to the air compressor only. You will need additional battery power to run whatever tool you are using with the inverter. Some air compressors also have limited power output support. Some can run on 12V and 120V, but others only support 120V.
Which Battery Should I Use?
It depends on how often you use the air compressor and what purpose. Lithium batteries have a higher discharge rate and superior performance compared to lead acid, but they are not always the right answer. For basic tasks the VMAX 50ah AGM battery will be enough.
If you mainly use a 12V air compressor to inflate tires and use it with a few tools, a lead acid battery is enough. There is no need to buy an expensive lithium battery when you only use the air compressor a few minutes a day. But you will need a powerful system to run a motor or a pump on an inverter.
But if you have a 2 HP air compressor and run it for an hour or more in a workshop, you will probably want to buy lithium batteries. The biggest benefit of lithium is you can fully discharge it, whereas with lead acid you only have access to half its capacity. When the level drops to 50% you have to recharge it.
That can be frustrating if you have a lot of work to do, so it is best to invest in a lithium battery. Some high end air compressors also require more power than an FLA battery can handle, so that is another reason.
There are some high quality lead acid batteries though, so if you do not mind the low discharge rate and maintenance, they are serviceable. It really comes down to what you need, how you operate an air compressor and power consumption.
Give yourself a week or two to run your devices. Note how often you use it, power consumption etc. This will give you an idea of what inverter and battery sizes to get. As always, add an additional 25% or so to the total just in case.
Conclusion
There is no need to be confused when it comes to running air compressors on an inverter. You just need to determine what compressor to use and its power requirement. With that information you can run the device with confidence.
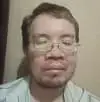
I am an advocate of solar power. Through portablesolarexpert.com I want to share with all of you what I have learned and cotinue to learn about renewable energy.